Why are Shark Vacuums So Hard to Repair?
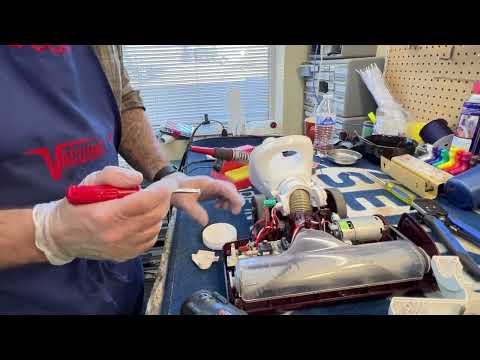
Repairing Your Shark Vacuum
If you’re trying to repair your Shark vacuum cleaner and are having trouble, you are not alone! Shark does not make their vacuum cleaners easy to repair for a number of reasons.
While Shark vacuums offer decent cleaning performance and fun features, their design and manufacturing choices make repairs very challenging – or even impossible – for consumers and even for vacuum stores.
In this article, we are going to go over why Shark vacuums are so hard to repair and the impacts that this has on consumers, their wallets, and the environment.
How Does Shark Make Repairs Tough?
In this video, Josh goes over some of the unique and crazy things that Shark does to make repairing their machines incredibly difficult and what impacts that has.
What Does Shark Do to Limit Repair?
Unique Screws

Shark vacuums use a specific type of screw known as security bits or security screws, which are designed to make casual repair very difficult. Security bits are specialized screw heads that require a corresponding screwdriver or bit set to be properly engaged. Unlike common screws, which can be easily turned with a standard screwdriver, security screws feature intricate patterns or non-standard shapes on their heads.
Shark vacuums also use several different sizes of security screws throughout the vacuum. This intentional difference in screw sizes adds yet another layer of complexity when it comes to Shark repair. It means that people who want to open the vacuum must not only have the correct security bit set, but also spend extra time selecting the right size of bit for each specific screw.
The use of both security screws and multiple sizes, prevents most households from attempting repair on their Shark vacuum cleaner. It also makes repair very time intensive for vacuum repair shops, which will make the overall repair cost higher.
Limited Parts
Another aspect of Shark vacuums is that they do not sell a wide range of repair components required for fixing their products. Unlike many other vacuum manufacturers that provide a wider selection of replacement parts, Shark’s offerings of parts is incredibly limited.
Due to this, Shark vacuum owners may have a $10 switch go bad and have no way to repair their machine. This means that instead of a relatively inexpensive repair, many Shark vacuum owners are forced to buy a whole new vacuum cleaner.
Delicate Plastic Tabs
In addition to the challenges posed by limited availability of repair components and security screws, Shark vacuums are now constructed with internal plastic tabs that hold the machine together. These plastic tabs act as clasps, effectively locking the vacuum’s components in place. Consequently, even if all the screws have been painstakingly removed, attempting to open the machine for repair can be a frustrating endeavor.
The presence of these internal plastic tabs adds an extra layer of complexity to the disassembly process. It requires additional effort and precision to release these clasps without causing damage to the vacuum’s housing or internal components. This design choice by Shark can be particularly frustrating for individuals who are confident in their repair skills and wish to access specific areas for maintenance or part replacement.
Conclusion on Shark Repair
In conclusion, the limited availability of repair components, the use of internal plastic tabs, and multiple sizes of security bits in Shark vacuums present a massive obstacle for owners seeking to repair their machines. While Shark vacuums are incredibly popular, the tactics used to make repair impossible ensure that Shark vacuum users are stuck in a cycle of purchasing new vacuums every few years. We recommend that you bring your Shark vacuum into a local vacuum store like us to see if repairs are possible and to check out other, better brands. You can stop by any of our three locations today!