SEWING MACHINE REPAIR & SERVICE
Get Your Sewing Machine Serviced!
When a machine is serviced properly, it will reduce wear and tear. As a result, it will cause less damage. An unidentified problem with a sewing machine can lead to even greater issues. This will cause more expenses, especially if you need to replace parts.
So, getting your sewing machine serviced regularly will help identify any prevailing troubles. Most problems we see at our sewing machine repair service in Boulder could have been avoided if the machine had been routinely serviced.



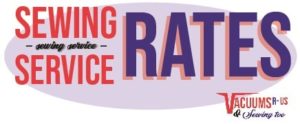
SEWING MACHINE SERVICE INCLUDES:
TENSION ADJUSTMENT, NEEDLE BALANCE, CLEANING, OIL, GREASE
SEWING MACHINE TYPE & SERVICE PRICE
MECHANICAL MACHINES $99.99
COMPUTERIZED MACHINES $149.99
SINGLE NEEDLE EMBROIDERY MACHINES $179.99
MULTI-NEEDLE EMBROIDERY MACHINES $279.99
LONG ARM MACHINES $249.99
SERGER/OVERLOCK MACHINES $149.99
FRONT OF HOUSE DIAGNOSTIC FREE
BENCH DIAGNOSTIC $45
Arvada
Vacuums R Us & Sewing Too –Â Arvada Store
5215 W. 80th Ave.
Arvada, CO 80003
(303) 455-3096
Hours
M-F: 9-7
Saturday: 9-5
Sunday: 10-4
Holidays: 10-4
Boulder
Vacuums R Us & Sewing Too – Boulder Store
3005 28th St.
Boulder, CO 80301
(303) 449-8913
Hours
M-F: 9-6
Saturday: 9-5
Sunday: Closed
Holidays: Closed
Fort Collins
Vacuums R Us & Sewing Too – Fort Collins Store
501 Riverside Ave.
Fort Collins, CO 80524
(970) 223-7327
HoursÂ
M-F: 9-6
Saturday: 9-5
Sunday:Closed
Holidays: Closed
$89.99 Mechanical Sewing machine tune up!
$89.99 Mechanical Sewing machine tune up*
* Parts extra. Restrictions apply. $139.99 for computerized machines.
Choose a method to receive this coupon and more!
By clicking “Sign up” you agree to allow us to send this coupon via the email or phone number you provide followed by a maximum of three text messages/month and/or 15 emails/year with related coupons, offers, and sales. Unsubscribe at any time by texting STOP or clicking unsubscribe. Message and data rates may apply.
We do not share our customer’s information with any other companies.
Sewing Machine Service & Repair
The creations you make with your sewing machine are an expression of yourself. When your machine needs repair or service there isn’t room for compromise. We service and repair all brands and all models of sewing machines, including Viking, Bernina, Pfaff, Juki, Janome, Baby Lock, Elna, Necchi, Brother, Singer, Kenmore and Bernette.
Our sewing machine services are all inclusive. Our factory trained technicians thoroughly inspect your sewing machine and make necessary adjustments to ensure your machine is returned to you in the best condition possible.
Vacuums R Us & Sewing Too – Arvada Store as well as our Boulder location Vacuums R Us & Sewing Too – Boulder Store have qualified technicians that will test thread delivery on your sewing machine to ensure there is no damage to the tension discs or check springs of your sewing machine. Tension is tested on your upper thread to ensure there is tension after being delivered through the sewing machine.

Did you know?! For optimal sewing performance, your sewing machine should be serviced by trained technicians every 12 to 18 months. Internal grease, lubrication and oil dries up over time. This can be a cause of excess lint and debris inside your machine soaking up the oil, or dry climates basically drying out the internal mechanisms of your machine. Without proper lubrication inside your sewing machine, the components that move internally will no longer move! When these components do not move, tons of issues can occur causing extensive repairs to your beloved sewing machine. A seized hand wheel can be the result of old grease that has dried and cracked an internal gear. If you want your sewing machine to run in tip top shape and continue creating beautiful projects, bring your sewing machine to either our Arvada or Boulder locations for a service or tune-up every 12 to 18 months by one of our factory trained technicians.
If your sewing machine requires more than a standard service or tune-up, our trained employees provide free estimates on the sewing repair needed before check in. Our front of house associates thoroughly check over your sewing machine while you are present. Our trained employees check to see if your sewing machine turns on and off and also check your handwheel to ensure the handwheel spins freely. Our trained employees then test the zig zag mechanism verifying there are no additional problems. We ask you to take home any additional accessories you may have brought with your machine, including sewing machine manuals, optional presser feet, accessory trays, spools of thread and spool caps. Our technicians will only need the standard presser foot, foot control, power cord, bobbin case and bobbin to complete your sewing machine tune-up or repair.
Once your sewing machine is in our technicians hands, our technicians ensure your sewing machine powers on and check for any burrs or damages to the needle plate, hook and bobbin case. Burrs can cause the thread to break when sewing, deformed stitching and tension issues.
Most built in needle threaders on a sewing machine have a tiny wire that pulls the thread through the eye of the needle. This tiny little wire can bend over time or if the built in needle threader is being used with some decorative threads, or smaller sized sewing machine needles. If your sewing machine has a built in needle threader, our certified technicians test the needle threader and make any necessary adjustments. If your sewing machine’s needle threader wire is severely damaged or missing and an adjustment cannot be made, replacement of the needle threader hook may be recommended.
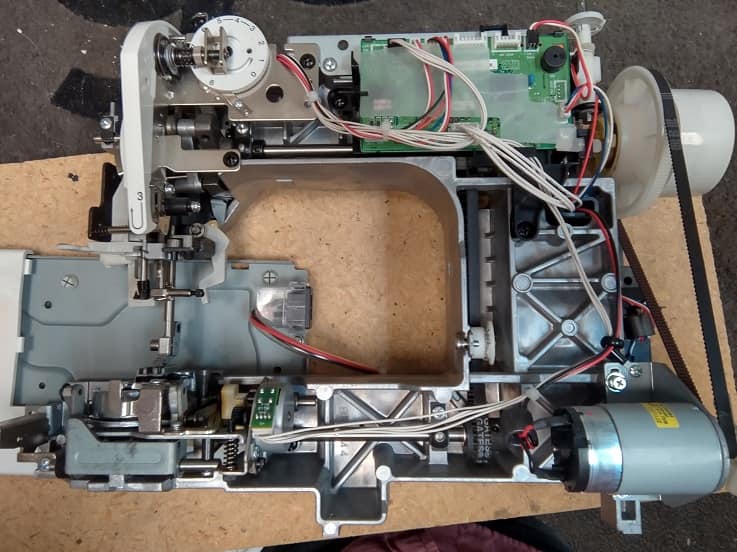
The bobbin winder on your sewing machine is tested for proper functionality, testing for proper tension and speed. The bobbin wound by our technicians is inserted into the bobbin case, where the technicians then check your sewing machines bobbin case tension. If there are any variances to proper bobbin tension, our trained technicians will make the necessary adjustment and restore your sewing machine’s tension.
Sewing machines feed material through the machine with the help of two long teeth protruding out from your needle plate area. When your sewing machines feed teeth, or feed dogs, do not move material through your sewing machine properly or evenly, there may be other repairs needed. Your sewing machines feed system is tested by our technicians to ensure the feed dogs are moving forward during standard sewing and backwards during reverse. If your sewing machine has the option to raise and lower the feed dogs, this mechanism is also tested. Most modern sewing machines have the option to raise and lower your sewing machines feed dogs for darning or free motion quilting.
Once all external components are inspected and tested by our qualified technicians, your sewing machine’s external cover is removed to begin the internal work on your sewing machine. With the covers removed, our certified technicians clean the internal sewing machine’s chastity by removing all dust, dirt, lint and debris. Any old and dried up grease and lubrication is also removed from your sewing machine gears and discs. After the sewing machine has been cleaned internally, our trained technicians apply new grease to the components requiring grease and apply oil to all necessary internal components.
Sewing machines require proper timing to form beautiful stitches. If the eye of your sewing machine needle does not enter the bobbin area at the precise time, your sewing machine will not form a stitch properly. Sewing machines form stitches by looping both the top thread and bobbin thread together, which is the result of the threaded sewing machine needle looping with the bobbin thread at the precise time. After your sewing machine has been cleaned and oiled internally, our factory trained technicians install a new needle into your sewing machine, check your sewing machines feed timing and retime your hook to ensure quality stitching on your sewing machine. The new needle is included in our service rates at no extra charge. Our technicians will also set your sewing machines needle bar height. Any variance in factory set needle bar height can alter your sewing machines stitching, resulting in skipped stitches, ticking sounds and not being able to pull your bobbin thread up consistently.
If your sewing machine is computerized, our factory trained technicians check your sewing machines firmware. Most sewing machine manufacturers release new updates to your computerized sewing machine frequently. Our repair technicians will install the latest updates to your computerized sewing machine so your machine is up to date.
The final process of our sewing machine service includes an exterior cleaning of your sewing machine. Our service technicians clean the outside of your sewing machine with an all natural cleaning agent, free of harmful chemicals.
Lastly, our technicians perform an extensive and final test sew of your sewing machine. Your sewing machine is ran for over one minute at its highest sewing speed. This ensures your sewing machine operates smoothly and also helps feed the oil through the machine. Our certified technicians will then sew several stitch samples on your sewing machine.
- Straight stitch to test your sewing machines stitch quality
- Reverse stitching to test the reverse mechanism of your sewing machine
- Zig-zag stitch to test your sewing machines needle bar mechanism
- Triple zig-zag stitch or a mending stitch to test your sewing machines needle positions 5. Decorative stitch to test overall functionality of sewing machine
At Vacuums R Us & Sewing Too – Arvada and Boulder, our trained service technicians provide quality sewing machine services and tune ups, and quality repairs. Bring your machine in to the experts who understand the importance of your sewing machine!