Elna sewing machine repair in boulder
Sewing machines, just like any other device, are prone to experience issues during their lifetime. Vacuums R Us & Sewing Too in Boulder can held you following a few good practices, and you can keep most of these problems at bay.
Â
Vacuums R Us & Sewing Too – Boulder Store
3005 28th St
Boulder, CO 80301
Corner of 28th & Valmont in front of Rayback Collective
(303) 449-8913
An unexpected problem will most likely halt all your sewing projects and have you frantically searching for a solution. One way of not running into any sudden issues is by getting your machine serviced regularly and having any problems fixed ASAP. Although some issues can be fixed alone, it’s always advised to have a trained set of eyes look into matters because you might end up causing more harm than good.
If you are looking for Elna sewing machine repair in Boulder, we at Vacuums R Us & Sewing Too–Boulder Store have a team of certified technicians ready to fix your sewing machine for you. With over 18 years of experience in Boulder sewing machine repairs, we are so confident about our work that we offer an irreversible 90-day service warranty to any sewing machine that passes our technician’s benches.
We fix and service all brands and types of sewing machines available and are also an authorized service center for some of the biggest brands such as Singer, Janome, Viking Husqvarna, Elna, and Elnitta.Â
$89.99 Mechanical Sewing machine tune up!
* Parts extra. Restrictions apply. $119.99 for computerized machines.
Choose a method to receive this coupon and more!
By clicking “Sign up” you agree to allow us to send this coupon via the email or phone number you provide followed by a maximum of three text messages/month and/or 15 emails/year with related coupons, offers, and sales. Unsubscribe at any time by texting STOP or clicking unsubscribe. Message and data rates may apply. We do not share our customer’s information with any other companies.
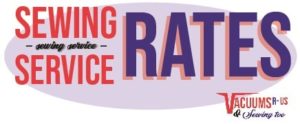
SEWING MACHINE SERVICE INCLUDES:
TENSION ADJUSTMENT, NEEDLE BALANCE, CLEANING, OIL, GREASE
SEWING MACHINE TYPE & SERVICE PRICE
MECHANICAL MACHINES $99.99
COMPUTERIZED MACHINES $149.99
SINGLE NEEDLE EMBROIDERY MACHINES $179.99
MULTI-NEEDLE EMBROIDERY MACHINES $279.99
LONG ARM MACHINES $249.99
SERGER/OVERLOCK MACHINES $149.99
FRONT OF HOUSE DIAGNOSTIC FREE
BENCH DIAGNOSTIC $45

4 Reasons To Get Your Sewing Machine Serviced
It’s a known fact that sewing machines need to be serviced by a certified professional every 12 to 18 months. But why does a sewing machine need to be serviced so often? Why would you need to hand over your sewing machine to a service center if it makes no trouble at all?
These are some valid questions and hopefully, we can shed some light on them.
Reduce Wear And Tear
A sewing machine comprises many moving parts, and these parts need proper lubrication and oil to run efficiently. However, with time, the oils lubricating these parts dry out.
The lack of proper lubrication will cause friction between the moving components which will lead to wear and tear. The dust and dirt that accumulates inside the machine in time will also cause issues. They will prevent the cogs and gears of the machine from moving as intended, which can lead to problems such as uneven stitches.
You can indeed clean and lubricate the sewing machine to some extent. But it won’t be that easy when you are dealing with the inner chassis of the machine which is best left for trained professionals. A minor mishap like cleaning liquid seeping into an unwanted partition will fry your sewing machine.
Fewer Expenses In The Long Run
When a machine is serviced properly, it will reduce wear and tear. As a result, it will cause less damage. An unidentified problem with a sewing machine can lead to even greater issues. This will cause more expenses, especially if you need to replace parts.
So, getting your sewing machine serviced regularly will help identify any prevailing troubles. Most problems we see at our sewing machine repair service in Boulder could have been avoided if the machine had been routinely serviced.
Longer Life Spans
It’s no surprise that a sewing machine lasts longer when it’s regularly maintained (only if it’s done right). Parts that function properly with minimum wear and tear will significantly reduce the risk of your sewing machine running into any trouble.
It’s also much easier to diagnose any problems that a regularly serviced sewing machine has. Imagine trying to find something in an attic that no one’s set foot in for over 3 years. It’s hard and will consume a lot more time than finding something in a well-kept room.
Our Sewing Machine Repair Process Simplified
Although a routinely serviced Elna sewing machine will provide you with an optimum sewing experience, you need to make sure that it is taken care of at an experienced and reputable service center. That’s exactly what we at Vacuums R Us & Sewing Too–Boulder Store offer. We’ve proved repeatedly that we are more than capable of handling all sewing machine needs and issues. So, let’s take a quick look at how our technicians go about repairing your sewing machine.

Exterior Inspection
Our technicians at the Boulder store are very methodical and prefer to work on things one at a time so that nothing is overlooked. First, they start with the exterior. They check if the sewing machine powers up and test if the power consumed by your sewing machine is up to standard. They also inspect the body of the unit for any burrs.
Burrs cause damage to the thread and also affect the tension in the thread distribution. They also make sure that none of the parts required to perform different functions are missing or damaged. Once all these factors are considered, our techs test out a series of stitches to further identify any issues.
Top Thread Analysis
After the exterior inspection, we evaluate the tension of the top thread. We examine the stress discs and the spring tension retention of the machine. Both the top thread and bottom thread go through a series of mechanisms depending on the type and brand of sewing machine you have.
So, we need to make sure that the thread goes through each part with no trouble to get the best sewing experience. A feature in many modern sewing machines is the built-in needle threader. It’s a wonderful piece of engineering for anyone having trouble getting thread into the eye of the needle.
We go through every bit of the mechanism to check if there are any bent cables or damaged parts to hinder its operation. And if we come across any problems, we will adjust it or suggest a replacement if required.
Bottom Thread Analysis
Next, our techs examine the bottom thread and all the mechanisms it passes through. The bobbin helps to feed the bottom thread evenly. They check the tension it gives and the speed it feeds the thread.
If they run into any problems, they make the necessary adjustments to get it back to optimum conditions. A bobbin that lacks tension and speed will ruin the stitches and can create overlapping or skipped stitches.
The Fabric Feed
Once our technicians are satisfied with the thread distribution in the machine, they move onto the feeding mechanism. The feeding mechanism is more commonly referred to as the feed dogs which comprise a pair of teeth that move.
The movement of the set of teeth depends on the type and brand of the machine. Usually, an Elna sewing machine has feed teeth that can move both forward and backward. Some models allow to change the feed dog elevation and also change the number of teeth. Our specialist notes every feature and makes sure that every one of them performs as expected.
Interior Inspection
After every external feature is examined, our certified technicians work their way into the inner parts of your sewing machine. First on the to-do list is a thorough internal clean-up. Our specialists get rid of every speck of dust and dirt they can find using an assortment of specialized tools.
They also replace the old oil and other lubricants so that the machine runs smoothly. They do this with extreme care because you need to apply the right lubricant to the right place. For example, applying oil to a part that needs grease is not ideal and may cause problems in the long run.
Once they are happy with the cleanup, they evaluate your sewing machine’s timing. This is probably the most important step of our sewing machine repair process.
A sewing machine with bad timing is just a device that bobs a needle. A typical sewing unit will use two threads to form a stitch. The bottom thread is run along with the fabric while a needle fastened to the top thread punctures the fabric. A shuttle hook then grabs hold of the top thread and creates a stitch. This process happens repeatedly to create stitches.
Therefore, the needle needs to be at the right location at the perfect time to make a stitch. Our techs look at the total mechanism and make the adjustments required to achieve flawless timing. Bad timing results in issues like skipping stitches, ticking sounds, and not having the ability to draw your bobbin thread up continually.
Final Inspection
Once we sort out every issue, we put back the covers and give it one final external clean-up. We use cleaners that are 100% natural so that there isn’t any damage done to the body. If you have an electronic sewing machine, you can trust us to install the latest update available when we hand it back to you.
Finally, we run a few tests to check if the sewing machine meets our expectations (which are pretty high, to be honest). A series of stitches (straight stitch, zig-zag stitches, ornamental stitches, and more) are tested out on your sewing machine. We will also conduct a speed test to confirm that your machine can run at its highest speed with no trouble.
We at Vacuums R Us & Sewing Too–Boulder Store pride ourselves in providing effective and long-lasting solutions to sewing machines with issues, especially Elna sewing machines. So, we are certain that our team of trained specialists will have the answer for your sewing machine troubles as well!