Powerstar Central Vacuum Repairs And Installations In Boulder
Powerstar has been a key player in the Central Vacuum arena for over four decades. Staying true to its name, each Powerstar central vacuum unit packs enough power to get any type of establishment sparkling clean. And as a bonus, its filtration system surpasses that of many other brands in today’s market.
Fortunately, despite the functionality the brand offers, Powerstar units have become more affordable over the years. And it has become the go-to brand for central vacuum needs in most countries worldwide.
However, similar to any other central vac, the performance of a Powerstar unit depends on its installation. The installation will determine how effective and power efficient the unit is. Further, proper installation will guarantee a longer life span and result in minimum repairs in the long run.
Over the years in service, we at Vacuums R Us & Sewing Too–Boulder Store have come across our share of terrible central vacuum installations. These installations were horrifying, with pipes and wires running amok within the walls. They were putting an enormous strain on the vacuum system, causing it to break down. Frankly, neither we nor the homeowners enjoyed the trouble of sorting out the mess to get the machine back on track.
So, if you plan on installing a central vacuum, we strongly suggest you employ a team of qualified professionals.
On that note, if you are looking for Powerstar Central Vacuum repair and installations in Boulder, we at Vacuums R Us & Sewing Too–Boulder Store are thrilled to offer you our services. Being in business for over 18 years, we’ve tackled both small and large-scale central vacuum projects in the Boulder area. And we’ve nailed every case we’ve handled so far.
We strongly believe that there’s no problem that experience and skill can not solve. The approach we take to repair and install central vacuums results from nearly two decades worth of trial and error. And this approach is what we will cover in the article.
Contact us to schedule a house call (303) 455-3096
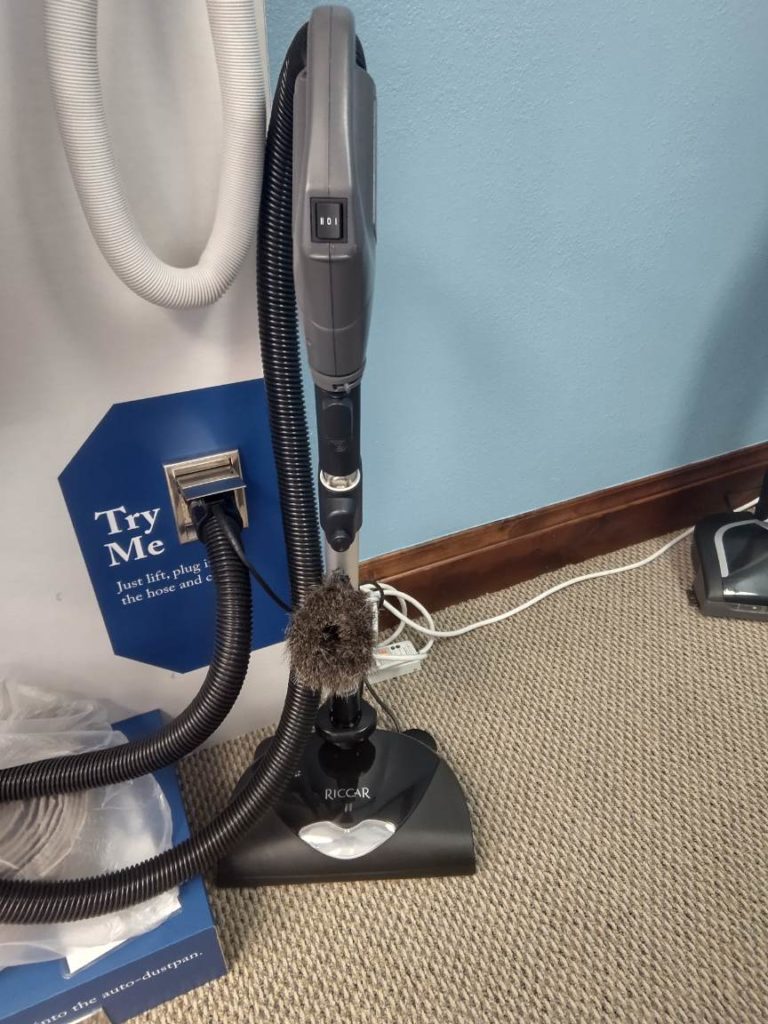
Our Powerstar Central Vacuum Installation Process Simplified
To keep things simple we’ve narrowed down our installation process to 5 stages. However, keep in mind that the process can expand beyond these steps depending on the complexity of the project at hand.The Action Plan
Similar to any project, you require a rock-solid plan of action for a central vacuum installation to succeed. The plan needs to cover all the bases of the system, including future repairs and renovations. Therefore, our skilled technicians plan the system before actually installing it. They might also require building plans at this stage if the establishment is large. While mapping out the best routes the vacuums pipes and wires can take, our techs also look out for existing installations. It will prevent them from damaging them during the central vac installation. Apart from assessing viable installation routes, our professionals map out the best inlet placement in each room. Properly, planning inlets will apply less pressure on the central unit and also cut down costs.Placing Inlets
Many believe that placing more inlets in a room can prove useful in the long run. We, however, strongly disagree. Installing excess inlets requires additional wires and pipes that will drive up installation costs. It will also make future system inspections during repairs much more troublesome. Therefore, we install inlets based on basic math. Considering the hose length and the area of each room, we determine the exact number of inlets a room needs. And once we figure out the number, we decide on the inlet placements based on the viable installation paths we drew up during the planning stage. When all is decided, we trace out the brackets on the walls and floor before cutting out the openings. We also place a marker close to the opening to help navigate the wires and pipes later on.Central Unit Installation
After installing the vacuum inlets, we mount the central unit in the lowest room of the building. This allows the machine to perform seamlessly as there’s no work done against gravity. Our techs then draw the wires from the central unit to the inlets installed in other rooms. Often, the wires of a central vacuum are of two types ~ signal wires and power cables. Both these wires need to work flawlessly for the machine to function at its best. The signal wires carry the “Switch on” and “Switch off” signals given through the hose at the inlets. So any issue with them will have you making trips to the basement every time you want to start or shut down the unit. Which, frankly, isn’t ideal. When wiring our techs also avoid running the wires over sharp edges. And if running a wire over a burr is their only option, they do their best to smoothen the surface. Once the wiring is sorted out, our experts move on to the pipework. With the previously placed markers serving as indicators, they navigate the walls till every pipe is connected to an inlet. Ideally, the central vac pipes need to be isolated from other installations. But as this is practically impossible, our skilled personnel use a variety of tools such as stud finders to locate empty spaces to run the pipes.It Does Not End Here…
When the inlets, wires, pipes, and the unit are all in place, we perform one last inspection to make sure that everything works as intended. We go over every aspect of the system once more to avoid any oversights. And also perform a series of tests to identify leaks, clogs, and other issues. The pipes are also stress-tested to make sure that they won’t loosen during operation. We then end the installation process when we are satisfied that everything is up to standard.The In-house Powerstar Central Vacuum Repair Strategy
It’s quite clear that we at the Boulder store take a systematic approach to install central vacs. So it’s no surprise that we have a few predetermined steps in our central vacuum repair strategy as well.
An Initial Checkup
All good central vacuum repair sessions require an initial checkup to determine issues. So that’s exactly what our skilled analysts do first.
They run the unit in different settings and compare the results with the benchmark values of the model. They also record the problems they find in this stage to measure how effective the repair session was later on.
Although we’ve had years of experience in the industry, we still believe that there might be more to learn in our trade. So it has become a habit to record our repair and maintenance sessions for later review.
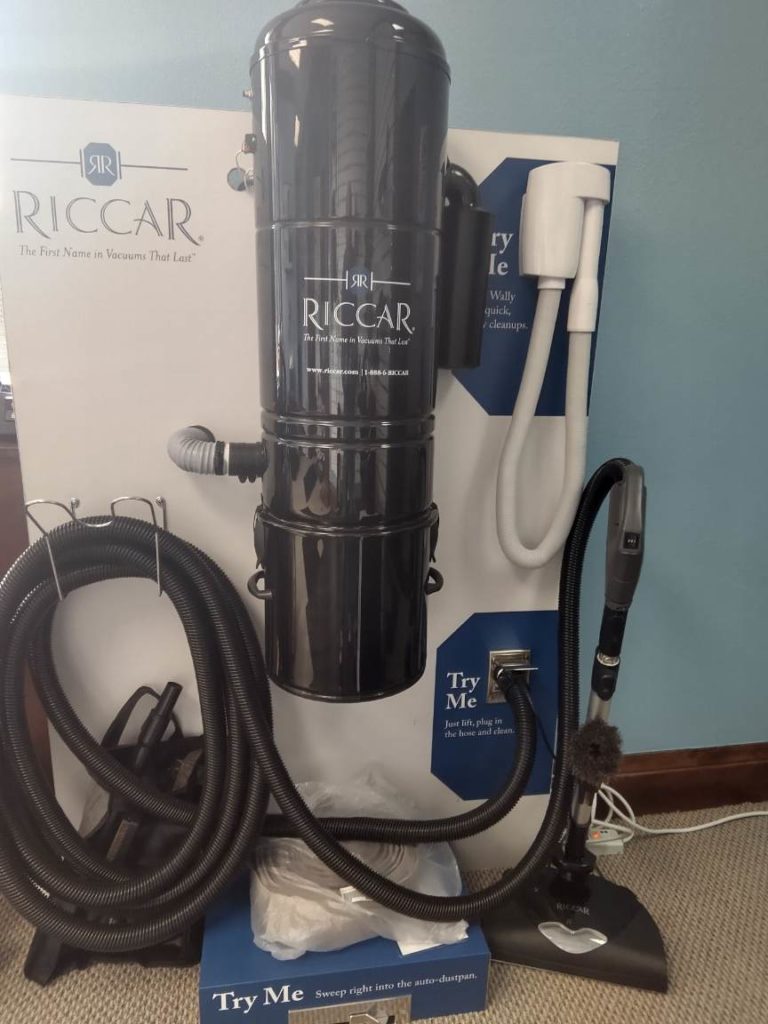
Power and Motor Inspection
Once we’ve figured out the problems, we immediately start working on the power-related issues. Power troubles are probably the worst type of problem we face, because any slip-up can end up frying the entire circuit board.
We start the process by examining the external wiring to make sure that the wiring is continuous with no split ends or burnt MCBs. Next, we strip off the covers and start working on the relays, power transformer, and circuitry inside the unit. Every component is tested using different tools, such as ammeters, to confirm that there aren’t any short circuits or power overloads.
When we are satisfied with the state of the electronics, we then inspect the motor for issues. Generally, most motor-related issues are caused by worn-out brushes. A quick replacement, however, ought to fix them. Yet, in extreme cases, there might be damages to the motor coils and internal structure.
At times like this, we try our best to restore the unit and might suggest a complete replacement if the motor is beyond repair.
Resolve Airflow Issues
After dealing with the problems related to the power and motor, we concentrate on the issues related to airflow.
A central vacuum works best only if it has a sufficient flow of air circulating the system. However, clogs and leaks along the pipes can impede airflow. So it’s necessary to deal with them if you want the unit to perform great.
Our technicians use various tools and techniques to identify these issues within the pipework. One popular technique they use to identify clogs is the “styrofoam ball test”. In this test, they introduce a few numbered styrofoam balls into the system and count them at the central unit’s collection tank. They can then, using any missing balls, figure out the pipeline which has a block.
The Ultimate Test
Usually, we end our central vacuum repair and maintenance session by testing the entire system one last time. We re-examine each issue we fixed and then do a thorough top-to-bottom inspection of the whole installation. We then run the unit and compare the status of the machine to its manufacturer’s benchmark values. If we find the results satisfying, we hand the central vacuum system back to you.
Although not in-depth, this is the process we follow during Powerstar Central Vacuum repairs and installations. The systematic approach we take allows us to be precise and not overlook any issue that needs fixing. Our method has been successful for nearly two decades and is yet to fail. So, if you are looking to install or repair a central vacuum, our doors at Vacuums R Us & Sewing Too – Boulder Store are always open to you.